Production Mode
Posted April 14, 2014

I love a plan. I love seeing the big picture and then filling in all the pieces to make it happen.
Back in the day I was a production manager for a couple of New York jewellery designers. Setting up systems for getting their work out by deadline was invaluable experience. A lot of it is common sense but I thought I’d share my process with you.
This is a plan for working on my line for an upcoming season – there are a few differences if you’re working towards existing orders (eg post trade show)
1. Decide which pieces to make and in what quantities.
I determine this by checking current stock levels and working out which favourites need topping up. Then comes the fun part where I wade through all the bits of paper where I’ve scribbled ideas for new designs. Lately I’ve also been taking photos of design ideas, which is a great way to get an immediate result. There’s always more than is possible to make so I usually make choices based on what is a natural flow on from the collection as well as interesting enough to keep me entertained!
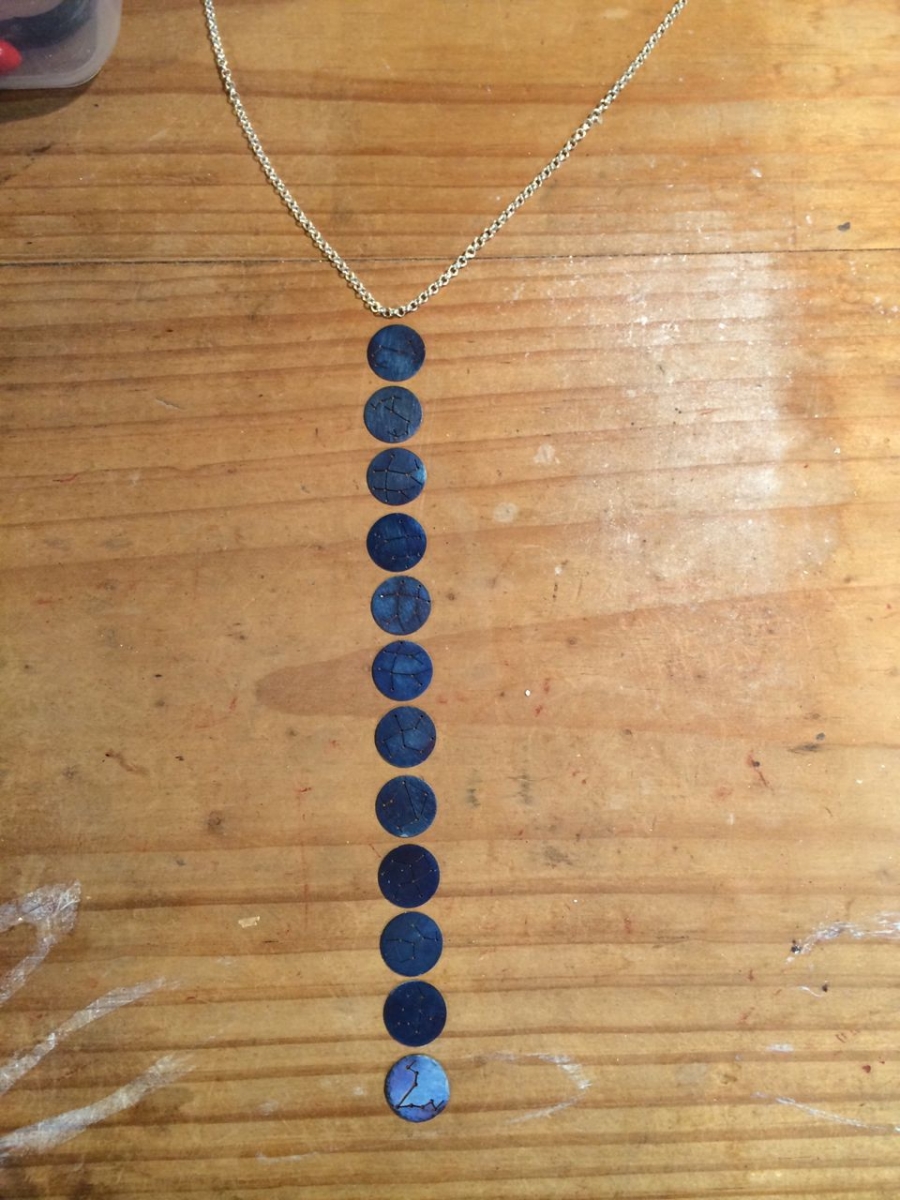
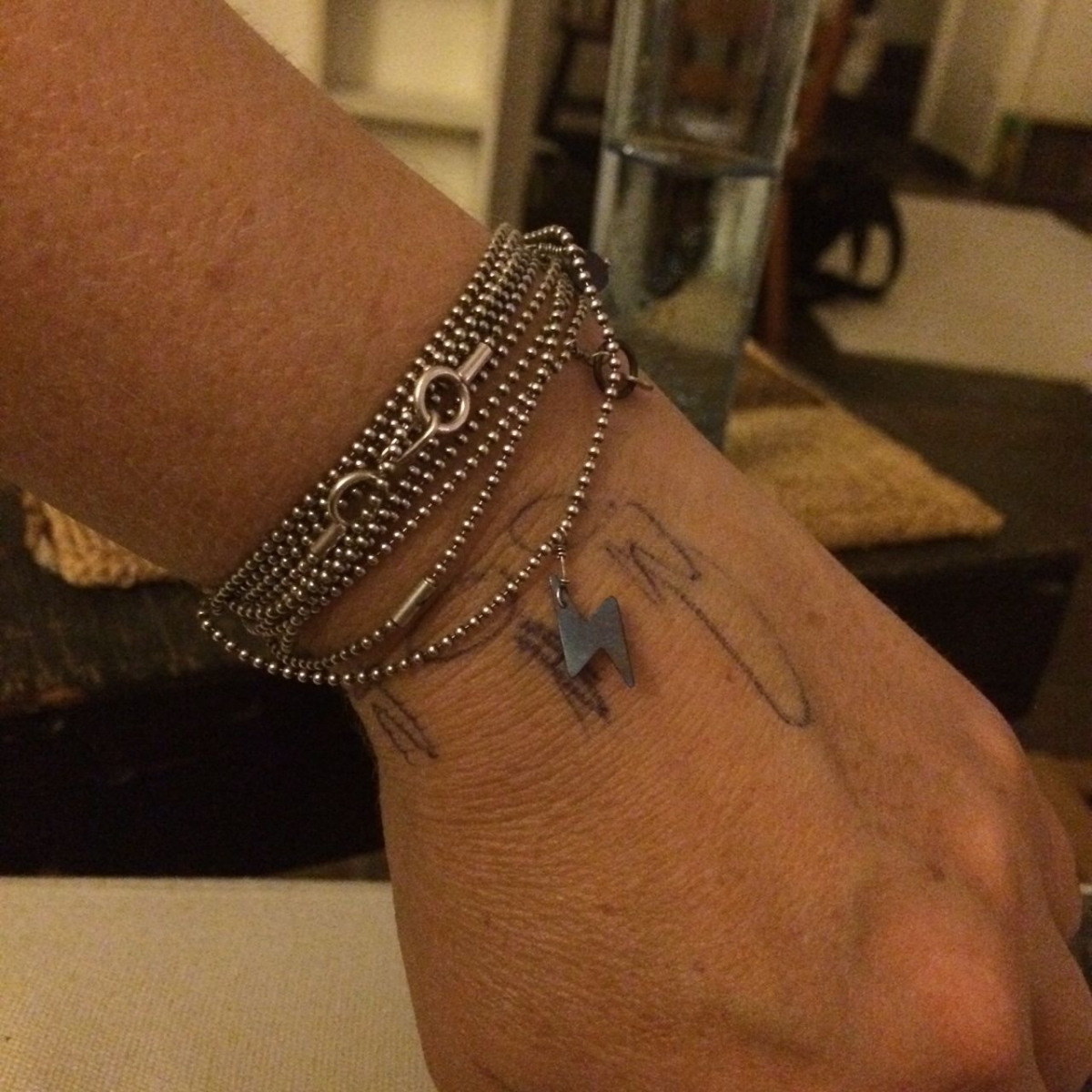
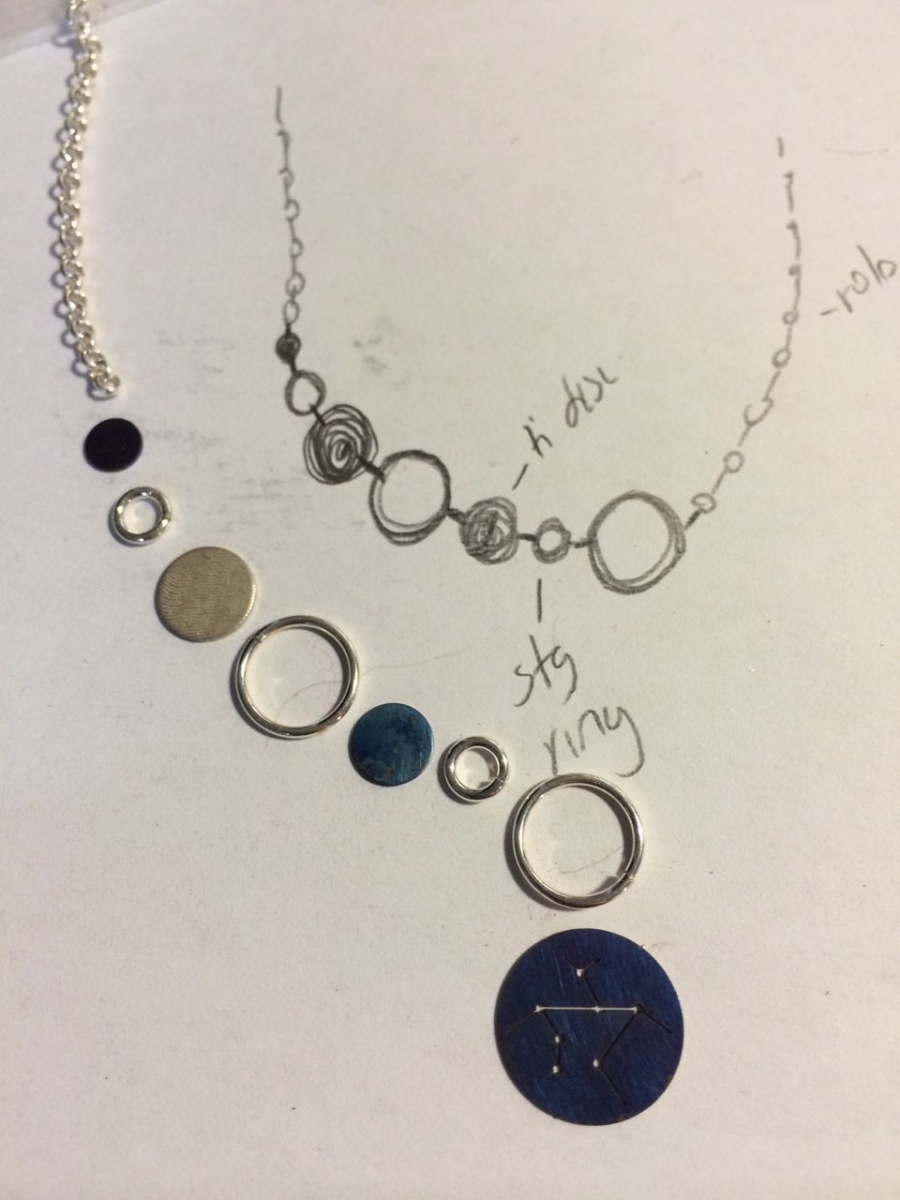
2. Establish the number of bench days between start and deadline.
At this point I usually make up a weekly calendar and block out bench days. I don’t spend a lot of time making anything fancy. There are plenty of organiser apps available but I find I get too distracted by them so I just stick to scrap paper with columns and dates.
Make sure to factor in life events and try and be as realistic as possible as to what you’re capable of.
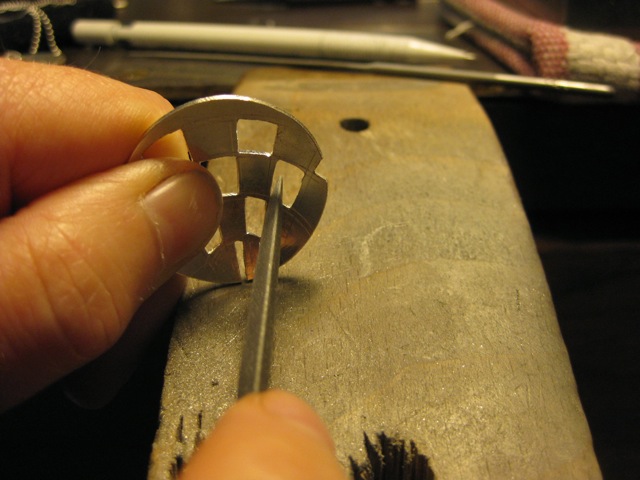
3. Allocate what pieces will be made on which days.
Being this specific is a good way to double check if your plan is actually do-able.
At this point it’s a good idea to look at your plan with an objective eye and tweak the number of pieces able to be made. I also find it helpful to leave a day or two for wiggle room where rollover work can fit in.
Breaking your production down to daily bite-size pieces is a great way to promote a sense of achievement rather than feeling swamped by the idea of a giant mass of unfinished work.
.jpg)
4. Order materials
Stocktake what materials you already have and work out the remainder needed to complete the production plan. I have a workbook that comes in handy here where I record the components needed for each piece, where they come from and a supplier code, if they have one. My workbook is an invaluable time saver, which I’ll outline in more detail on a future blog.
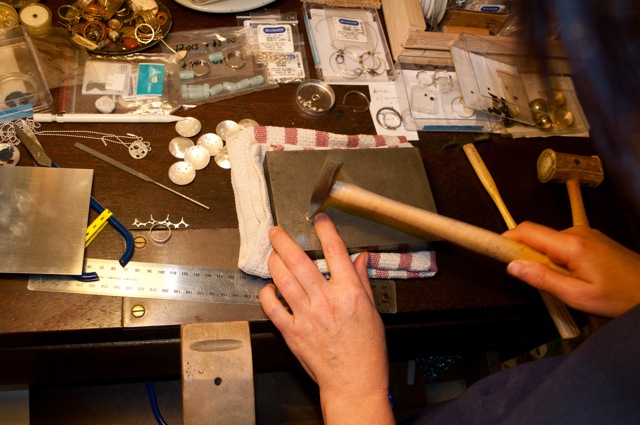
6. Get cracking!
Sit at your bench and make a bunch of cool work!!
.jpg)
TIPS:
- It’s good to mix it up to keep you on your toes and avoid boredom BUT try to keep it in a reasonably similar vein because you can waste a lot of time jumping all over the place with different tools and techniques.
-
You can end up getting super focused working to a plan which makes for a stiff body so make sure you stretch, drink water and blink (!).
In biz share...
Tags
- on the bench... (12)
- beyond the Bay... (11)
- inspired by... (6)
- in the Bay... (4)
- year of the brooch... (4)
- biz share... (3)
- tasty treats... (1)
Archives
- July 2016 (1)
- December 2015 (2)
- June 2015 (1)
- May 2015 (1)
- April 2015 (2)
- March 2015 (3)
- February 2015 (1)
- January 2015 (1)
- December 2014 (1)
- September 2014 (1)
Comments
Post new comment